داخل تراشی (بورینگ) | فرآیند، ابزارها و نکات کلیدی در ماشینکاری دقیق
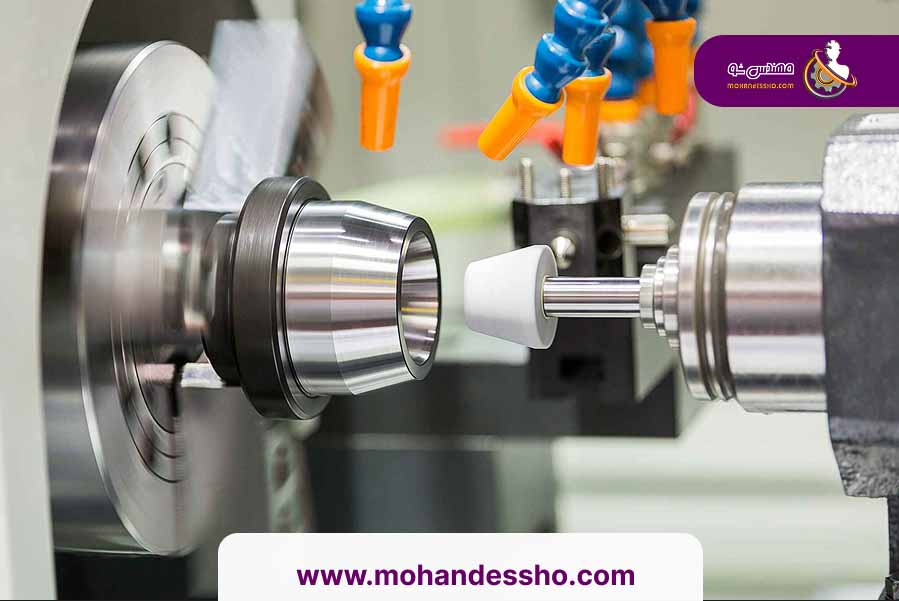
داخل تراشی (بورینگ) یکی از فرآیندهای مهم و تخصصی در حوزه ماشینکاری است که به منظور افزایش دقت ابعادی، بهبود کیفیت سطح و ایجاد سوراخهایی با قطرهای بزرگتر یا شکلهای خاص در قطعات استفاده میشود. این فرآیند معمولاً پس از سوراخکاری اولیه انجام میشود. تفاوت اصلی داخلتراشی با سوراخکاری در این است که سوراخکاری عمدتاً برای ایجاد سوراخهای اولیه و با دقت کمتر به کار میرود، در حالی که داخلتراشی برای رسیدن به ابعاد دقیقتر، هندسههای پیچیدهتر و کیفیت سطح بالاتر استفاده میشود. دستگاه داخل تراشی نقش بسزایی در پیشبرد فناوریهای مدرن به خصوص در صنعت خودروسازی و هوافضا ایفا میکند. در ادامه بیشتر درباره داخل تراشی چیست و چه کاربردی دارد؟ و تفاوت بین سوراخکاری و داخل تراشی صحبت خواهیم کرد.
فهرست مطالب
داخل تراشی (بورینگ) چیست؟
داخل تراشی (بورینگ) ابزاری است که قابلیت انجام عملیات متنوعی مانند سوراخکاری، فرزکاری، کنترسینک، روکشکاری، رولپلاکزنی، رزوهکشی و… را فراهم میکند. این دستگاه در مدلهای مختلف برای فضاهای کوچک، متوسط و بزرگ طراحی شده است. از این دستگاه عمدتاً برای گسترش سوراخهای موجود و ایجاد سوراخهای دقیق و صاف در قطعات استفاده میشود. ابزارهای تک نقطهای که به دوک چرخان متصل هستند، به صورت دایرهوار در اطراف سوراخهای موجود حرکت میکنند. قطر سوراخ ایجاد شده توسط این ابزارها از طریق تنظیم سر بورینگ کنترل میشود. چرخهای سنگزنی نیز حرکتی سیارهای دارند و به سرعت حول محور خود میچرخند؛ در حالی که به آرامی حول محور دوک حرکت میکنند.
در کارگاههای ابزارسازی، این دستگاهها معمولاً مجهز به یک دوک عمودی و یک میز نگهدارنده هستند که امکان حرکت افقی در دو جهت عمود بر هم را فراهم میکنند تا فاصله بین سوراخها با دقت بالا تنظیم شود. در برخی مدلها، خطای فاصلهای کمتر از 0.002 درصد گزارش شده است. در کارخانههای تولید انبوه، ماشینهای حفاری با دوکهای متعدد به طور گسترده مورد استفاده قرار میگیرند.
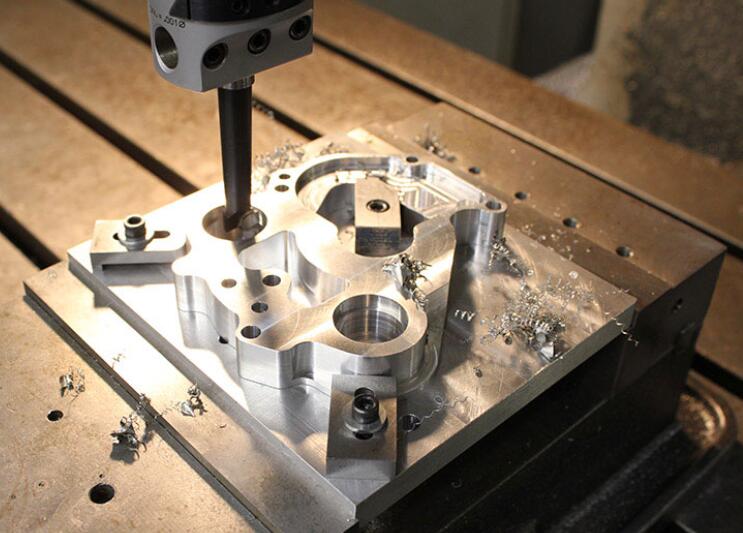
انواع فرآیندهای داخل تراشی
داخل تراشی خشن و پرداختکاری
در داخل تراشی خشن، ابتدا یک سوراخ اولیه به وسیله یکی از روشهای برادهبرداری، دریلکاری، ریختهگری یا آهنگری در قطعه ایجاد شده است. این سوراخ کوچک به عنوان نشانگر مختصات دقیق سوراخ عمل میکند. در مرحله بعد، با انجام عملیات بورینگ، سوراخ بزرگتر میشود. به عنوان مثال، اگر قطر مورد نیاز سوراخ 50 سانتیمتر باشد، تنها 5 سانتیمتر از آن قبلاً ایجاد شده و شما باید قطر سوراخ را 45 سانتیمتر افزایش دهید. در واقع، مسئولیت اصلی این کار بر عهده شماست. در فرآیند پرداخت کاری، هدف اصلی بهبود کیفیت و دقت سوراخ است. به طور مثال، اگر قطر نهایی سوراخ باید 10 سانتیمتر باشد و 9.5 سانتیمتر آن قبلاً تراشیده شده است؛ روشهای سنتی مانند دریلکاری یا آهنگری نمیتوانند دقت لازم را برای رسیدن به قطر دقیق فراهم کنند. در چنین شرایطی، از بورینگ برای پرداخت نهایی قطعه و افزایش دقت سوراخ استفاده میشود.
بورینگ دستی و CNC
بورینگ (Boring) فرآیندی است که برای بزرگتر کردن یا دقیقتر کردن سوراخهای موجود در قطعات استفاده میشود. دستگاه داخل تراشی به دو نوع اصلی تقسیم میشوند:
- بورینگ دستی: این نوع دستگاهها به صورت مکانیکی و با دخالت مستقیم اپراتور کار میکنند. دقت این دستگاهها به مهارت اپراتور بستگی دارد و معمولاً برای پروژههای کوچکتر و کمهزینهتر استفاده میشود.
- بورینگ CNC: این دستگاهها با استفاده از سیستمهای کنترل عددی، عملیات را با دقت بسیار بالا انجام میدهند. از ویژگیهای آنها میتوان به سرعت بالا، قابلیت تکرارپذیری و توانایی انجام عملیات پیچیده اشاره کرد. این دستگاهها در صنایع خودروسازی، هوافضا و تولید ابزارهای صنعتی کاربرد دارند
داخل تراشی با ماشین تراش و دستگاههای اختصاصی
داخل تراشی فرآیندی است که برای ایجاد یا بهبود اشکال دایرهای داخلی در قطعات توخالی یا سوراخهای موجود استفاده میشود. این عملیات میتواند با ماشین تراش یا دستگاههای اختصاصی بورینگ انجام شود. در روش ماشین تراش، قطعه کار روی سهنظام یا چهارنظام دستگاه تراش نصب میشود و ابزار برش به داخل قطعه نفوذ میکند. این روش برای قطعات کوچک و متوسط مناسب است. دستگاههای اختصاصی بورینگ نیز برای قطعات بزرگتر و عملیات پیچیدهتر طراحی شدهاند. آنها میتوانند به صورت افقی یا عمودی باشند و قابلیتهایی مانند پیشانیتراشی، شیارزنی و پخزنی را نیز ارائه میدهند
مقایسه بین روشهای مختلف بورینگ
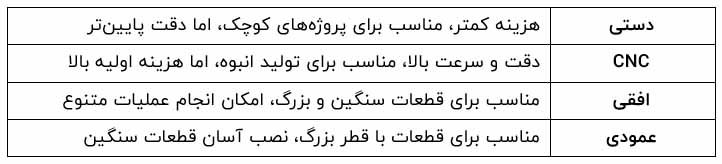
این مقاله بخشی از مبحث ابزارشناسی دوره آموزشی مسترکلاس آموزش ماشینکاری CNC است.
برای یادگیری صفر تا صد ماشینکاری تراش و فرز CNC روی لینک زیر کلیک نمائید.
ابزارهای داخل تراشی
داخل تراشی (بورینگ) ابزارهای مختلفی دارد که از چند منظر طبقه بندی میشوند:
انواع ابزار از نظر نحوه عملکرد
از نظر نحوه عملکرد، ابزار بولینگ به صورت زیر تقسیم میشود:
ابزار تک لبه: این نوع ابزارها به شکل مکانیکی روی میله دستگاه قرار میگیرند و برای جبران فرسایش مورد استفاده قرار میگیرند.
ابزار دو لبه: برای بهبود دقت در فرآیند سوراخکاری با دستگاه فرز بورینگ CNC، از ابزارهای دو لبه استفاده میشود که قادر به اعمال نیروی متعادل روی میله هستند و به این ترتیب امکان دستیابی به تلرانسهای دقیقتر را فراهم میکنند. با این حال، در صورت نیاز به تیزکاری، باید این ابزارها را جدا کرده و مجدداً نصب کنید.
ابزار تیغهای: این دسته از ابزارهای ماشین فرز بورینگ روی بدنه دستگاه نصب میشوند و قادرند سرعت پیشروی را به میزان قابل توجهی افزایش دهند. همچنین، به دلیل داشتن دو لبه برشی، از این ابزارها برای بهبود دقت و دستیابی به تلرانسهای دقیقتر استفاده میشود.
انواع ابزار از نظر جنس
بسته به نوع قطعاتی که دستگاه داخل تراشی (بورینگ) روی آنها کار میکند، نیاز به ابزارهایی با جنسهای متفاوت خواهد بود. در این زمینه، بهترین ابزارها برای داخل تراشی فلزات شامل موارد زیر است:
HSS: ابزار HSS (فولاد تندبر) در داخلتراشی یا بورینگ برای ایجاد سوراخهای دقیق و بزرگتر کردن سوراخهای موجود استفاده میشود. این ابزار به دلیل مقاومت بالا در برابر حرارت و سایش، برای تراشکاری فلزات مختلف مناسب است. طراحی آن به گونهای است که دقت و کیفیت بالایی در عملیات ماشینکاری ارائه میدهد.
ابزار کاربیدی: این نوع ابزار برای عملیات با سرعت پایین مناسب است و قادر است دقت دستگاه را به خوبی تنظیم کند.
ابزار سرامیکی: این ابزار در سرعتهای بالا به کار میرود و باعث کاهش سایش میشود. توصیه میشود از ابزارهای سرامیکی برای فرزکاری مواد آلومینیومی، برش مواد شکننده و ایجاد برشهای ناپیوسته استفاده نشود.
در انتخاب ابزار مناسب برای داخل تراشی (بورینگ)، استحکام و مقاومت ابزار نقش کلیدی دارند؛ زیرا این ویژگیها مانع از تغییر شکل یا شکست ابزار در برابر نیروهای برشی بالا میشوند. همچنین، مقاومت بالا در برابر سایش و حرارت، عمر ابزار را افزایش داده و کیفیت سطح قطعه را حفظ میکند.
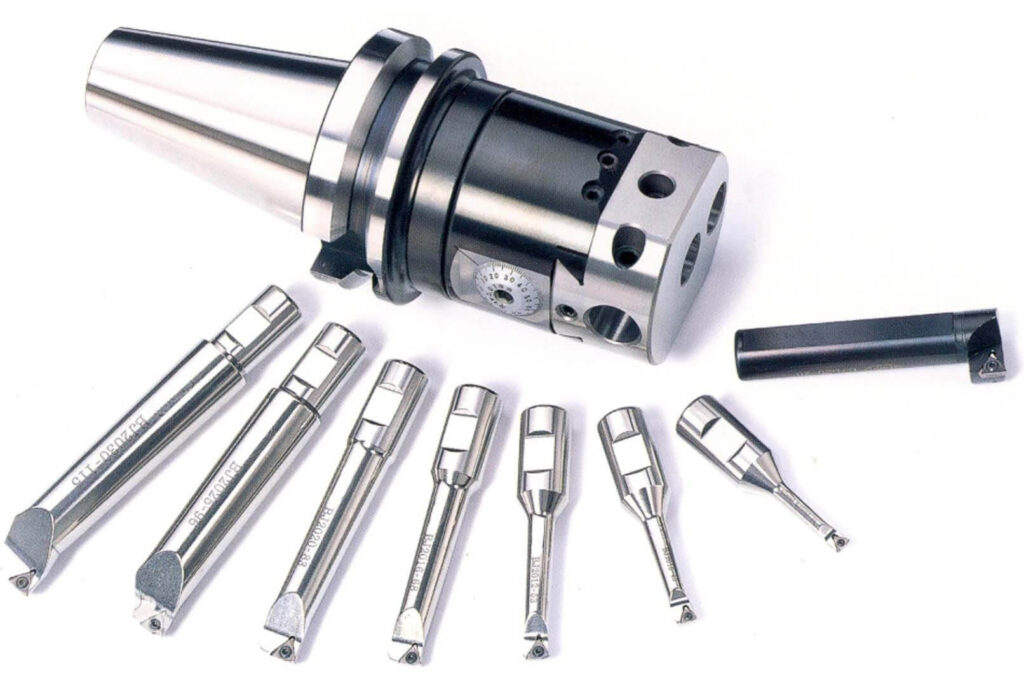
تنظیمات و پارامترهای مهم در داخل تراشی
سرعت برش و نرخ تغذیه از مهمترین پارامترهای ماشینکاری در داخلتراشی هستند. سرعت برش به میزان حرکت ابزار نسبت به قطعه کار اشاره دارد و معمولاً بر حسب متر بر دقیقه اندازهگیری میشود. این پارامتر تأثیر مستقیمی بر کیفیت سطح و طول عمر ابزار دارد. نرخ تغذیه نیز فاصلهای است که ابزار در هر دور چرخش قطعه کار طی میکند و بر زمان ماشینکاری و صافی سطح تأثیر میگذارد. همچنین زاویه و جهت حرکت ابزار در داخل تراشی (بورینگ) نیز نقش کلیدی در کیفیت و دقت عملیات دارند. زاویههای مختلف ابزار، مانند زاویه براده، زاویه آزاد و زاویه گوه، بر نحوه برادهبرداری و کاهش اصطکاک تأثیر میگذارند. زاویه تنظیم نیز که بین لبه برنده ابزار و سطح کار قرار دارد، میتواند بر عرض براده و فشار وارد بر ابزار تأثیر بگذارد.
برای کاهش ارتعاشات در فرآیند بورینگ، تکنیکهای مختلفی وجود دارد. استفاده از دمپرهای ارتعاشی یکی از روشهای مؤثر است که میتواند دامنه ارتعاشات را کاهش دهد و کیفیت سطح را بهبود بخشد. همچنین، استفاده از ابزارهایی با نسبت طول به قطر مناسب و طراحی سیستمهای کنترل فعال ارتعاشات، مانند عملگرهای الکترومغناطیسی، میتواند به کاهش ارتعاشات کمک کند.
کاربردهای داخل تراشی در صنایع مختلف
کاربردهای دستگاه داخل تراشی (بورینگ) در صنایع مختلف بسبار گوناگون است. در ادامه با برخی از کاربروهای این دستگاه آشنا میشوید:
کاربرد در ساخت قطعات دقیق مهندسی
داخل تراشی (بورینگ) یکی از فرآیندهای کلیدی در تولید قطعات دقیق مهندسی است. این فرآیند به دلیل دقت بالا و توانایی ایجاد تلرانسهای بسیار کم، در ساخت قطعاتی که نیاز به هماهنگی دقیق دارند، مانند اجزای ابزارهای اندازهگیری، تجهیزات پزشکی و دستگاههای الکترونیکی، استفاده میشود. داخلتراشی امکان ایجاد سطوح داخلی با کیفیت بالا و بدون نقص را فراهم میکند.
داخل تراشی در صنعت خودروسازی و ساخت قطعات موتور
در صنعت خودروسازی، داخل تراشی (بورینگ) برای تولید قطعاتی مانند سیلندرها، بوشها، و اجزای سیستم انتقال قدرت استفاده میشود. این فرآیند به دلیل توانایی در ایجاد سطوح داخلی با دقت بالا و کاهش اصطکاک، نقش مهمی در بهبود عملکرد و افزایش طول عمر قطعات موتور دارد. همچنین، دستگاه داخل تراشی در تولید قطعاتی که نیاز به مقاومت بالا در برابر فشار و حرارت دارند، مانند اجزای توربوشارژرها و سیستمهای خنککننده، کاربرد گستردهای دارد.
استفاده از داخل تراشی در صنعت هوافضا و قالبسازی
در صنعت هوافضا، داخل تراشی (بورینگ) برای تولید قطعاتی که نیاز به دقت بالا و وزن کم دارند، مانند اجزای موتورهای جت و سیستمهای هیدرولیکی، استفاده میشود. این فرآیند به دلیل توانایی در ایجاد سطوح داخلی با کیفیت بالا و کاهش وزن قطعات، در بهبود کارایی و کاهش مصرف سوخت هواپیماها نقش مهمی دارد. در قالبسازی نیز، دستگاه داخل تراشی برای تولید قالبهای دقیق و با دوام که در فرآیندهای تولید انبوه استفاده میشوند، به کار میرود.
مشکلات رایج و راهکارها در داخل تراشی
یکی از چالشهای اصلی در فرآیند ماشینکاری با دستگاه فرز بورینگ، ایجاد ارتعاش در این ماشینها است. در چنین شرایطی، لازم است با به کارگیری روشهایی این ارتعاشات را کاهش دهید تا دقت دستگاه حفظ شود. بهترین راهکارهایی که برای کاهش لرزش در حین کار با دستگاه فرز بورینگ CNC توصیه میشوند، عبارتند از:
- توزیع مناسب نیروهای برشی با کاهش زاویه برادهبرداری
- بالانس کردن دستگاه از طریق همراستا کردن محور دوران فرز بورینگ با مرکز ثقل قطعه
- استفاده از یاتاقانهای بدون اصطکاک
- اطمینان از سلامت تسمههای انتقال نیرو
- بازرسی منظم دستگاه فرز بورینگ برای کاهش لقی قطعات متحرک
همچنین برای دستیابی به نتایج بهتر دربهبود دقت و کیفیت سطح در بورینگ میتوانید به نکات مهمی مانند انتخاب ابزار مناسب از جمله کاربید یا الماس، کنترل ارتعاشات، اعمال بهترین تنظیمات دستگاه داخل تراشی برای دقت بالاتر، استفاده از روانکارها، کنترل کیفیت مداوم و… توجه داشته باشید.
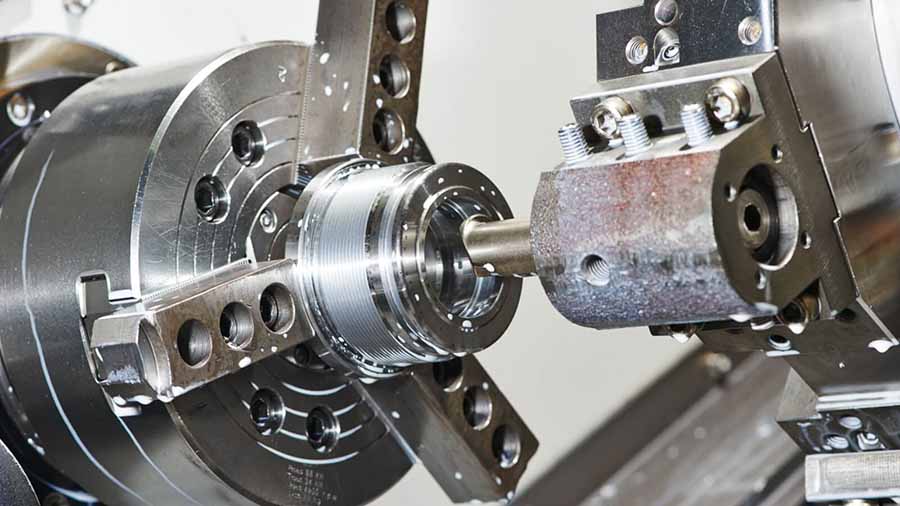
نکات ایمنی هنگام کار با دستگاههای داخل تراشی
ایمنی در کار با دستگاههای داخل تراشی (بورینگ) بسیار مهم است، زیرا این دستگاهها میتوانند خطرات جدی برای اپراتورها ایجاد کنند. به همین خاطر بهتر است به نکات ایمنی زیر توجه کنید:
-
استفاده از عینک ایمنی: هنگام کار با دستگاههای داخل تراشی، برادههای فلزی ممکن است به چشم پرتاب شوند. استفاده از عینک ایمنی استاندارد ضروری است.
-
استفاده از دستکش مقاوم: برای جلوگیری از بریدگی یا آسیب به دستها، دستکشهای مقاوم در برابر برش پیشنهاد میشود. البته در برخی موارد، استفاده از دستکش ممکن است خطر گیر کردن در دستگاه را افزایش دهد؛ بنابراین باید با احتیاط استفاده شود.
-
پوشیدن لباس مناسب: باید لباسهای تنگ و بدون آویز بپوشید تا از گیر کردن در دستگاه جلوگیری شود.
-
تنظیم سرعت مناسب دستگاه: سرعت دستگاه باید متناسب با نوع ماده و ابزار تراش تنظیم شود. سرعت بالا ممکن است باعث گرم شدن بیش از حد ابزار و قطعه کار شود که خطر شکستگی ابزار یا آسیب به قطعه را افزایش میدهد.
-
استفاده از خنک کنندهها: خنک کنندهها برای کاهش دما و جلوگیری از تغییر شکل قطعه کار و همچنین افزایش عمر ابزار تراش ضروری هستند. استفاده از خنک کنندههای مناسب و اطمینان از جریان کافی آنها در طول فرآیند تراشکاری اهمیت دارد.
نتیجهگیری
داخل تراشی (بورینگ) به عنوان یکی از فرآیندهای کلیدی در ماشینکاری، نقش حیاتی در صنایع پیشرفته مانند خودروسازی و هوافضا ایفا میکند. این فرآیند نه تنها دقت ابعادی و کیفیت سطح قطعات را بهطور چشمگیری بهبود میبخشد، بلکه با کاهش نیاز به عملیات تکمیلی و افزایش طول عمر قطعات، به کاهش هزینههای تولید کمک میکند. برای دستیابی به بهترین نتایج، انتخاب ابزار مناسب برای بورینگ از جمله جنس ابزار، سرعت برش و نوع ماشینابزار، امری ضروری است. استفاده از فناوریهای نوین و بهروزرسانی تجهیزات میتواند دقت و کارایی این فرآیند را افزایش دهد.
سوالات متداول
1- تفاوت داخل تراشی (بورینگ) و سوراخکاری چیست؟
سوراخکاری فرآیندی است که برای ایجاد سوراخهای اولیه با دقت نسبتاً پایینتر استفاده میشود، در حالی که داخل تراشی (بورینگ) فرآیندی تکمیلی است که برای دستیابی به دقت ابعادی بالا، بهبود کیفیت سطح و ایجاد سوراخهایی با قطرهای بزرگتر یا هندسههای پیچیدهتر به کار میرود.
2-چگونه ابزار مناسب برای داخل تراشی (بورینگ) انتخاب کنیم؟
انتخاب ابزار بورینگ به عوامل مختلفی مانند جنس قطعه کار، دقت مورد نیاز، سرعت برش و نوع دستگاه داخلتراشی بستگی دارد. ابزارهای با جنس کاربید یا الماس برای مواد سخت و دقیق مناسبتر هستند، در حالی که ابزارهای فولادی برای کاربردهای عمومیتر استفاده میشوند.
3- دستگاه داخل تراشی چه ویژگیهایی باید داشته باشد؟
دستگاه داخلتراشی باید دارای دقت بالا، قابلیت کنترل سرعت و پیشروی دقیق و سیستمهای خنککاری کارآمد باشد. دستگاههای CNC برای دستیابی به دقت و تکرارپذیری بالا در فرآیند بورینگ بسیار مناسب هستند.
دیدگاهتان را بنویسید